And the winners are…
On 5 December 2024, the FEDIL Innovation Award ceremony was held in the presence of Lex Delles, Minister for the Economy, SMEs, Energy and Tourism, numerous guests, members of the jury and the winners of the 2024 edition.
For this 26th edition of the FEDIL Innovation Award, no fewer than 33 projects were submitted, from which the jury, made up of experts from the public and private sectors, awarded four prizes:
- Innovation Award 2024 in the « Product » category : IEE S.A. for its « Laminated Busbar Connector »
- Innovation Award 2024 in the « Process » category : Husky Technologies for its « Plate Line Automation » project
- Innovation Award 2024 in the « Digital / AI » category : Creos Luxembourg S.A. / Datathings S.A for their project « Kopr: The AI Twin of the Smart Grid »
- Innovation Award 2024 in the « Engineering Excellence » category : CTI Systems S.à r.l / GRADEL S.à r.l. for their « On Board Cargo Loader »
The four winning projects fully meet the criteria set out in the Innovation Award rules, i.e. they stand out for their innovative and original nature, while being of interest to the Luxembourg economy. The Innovation Award was created by FEDIL in 1982 to encourage creativity, innovation and research in companies. The prize rewards innovators and researchers working for companies, as well as independent innovators and young researchers. The Innovation Award is attributed alternately each year with the FEDIL Environment Award.
You will find a detailed description of the winning projects in the following pages.
A committed message for innovation
Georges Rassel’s welcome address at the FEDIL Innovation Award 2024 ceremony emphasised the pivotal role of innovation in shaping the future of Luxembourg’s industries. Here are the key takeaways:
With global challenges, including geopolitical shifts and heightened competition, European industries need a united strategy to maintain technological sovereignty, bolster supply chains, and pursue innovation. The recent Draghi Report underscores the urgency of such efforts.
Technologies like AI, Big Data, IoT, and robotics are reshaping industries, demanding not just tech adoption but operational reinvention and cultural shifts. Platforms such as Luxembourg Digital Innovation Hub (DIH) and Digital Learning Hub (DLH) are crucial but underutilised. More effort is needed to empower SMEs in their digitalisation journeys. As interconnectedness grows, cyber threats pose significant risks. Public-private collaboration, information sharing, and workforce training are essential to fortify defenses. Luxembourg’s initiatives, like acquiring an AI-optimised supercomputer and supporting quantum computing, aim to lead in digital innovation.
In the field of energy transition, the fight against climate change aligns with industrial innovation, offering prospects in cleaner technologies and green markets. Strategic partnerships, especially in renewable energy, hydrogen, and carbon capture, are key.
To turn these challenges into opportunities, European regulations must balance harmonisation with industrial flexibility, avoiding excessive administrative burdens that stifle creativity and growth.
FEDIL has long been an advocate of collaborative research. Proposals like establishing a science and technology park near Belval highlight the need for synergy between academia, research institutions, and industries to address modern challenges effectively.
The overarching message was clear: innovation is not just a tool but a necessity for Luxembourg’s industries to navigate challenges, seize opportunities, and secure a prosperous future. Through collaboration, strategic investments, and policy support, the nation can continue to thrive amidst global shifts.
In his speech, Georges Rassel praised the high quality of the projects submitted for the competition, which provided an impressive illustration of the industry’s strength in innovation, with entries from companies of all sizes, from start-ups to multinationals, and from a wide range of sectors. The FEDIL Innovation Award honors creativity and the ability to turn ideas into growth engines. The awarded projects exemplify perseverance, vision, and the transformative power of innovation. They inspire industries to push boundaries and foster sustainable growth. This year’s record 33 applications reflected advancements in digital transformation, AI, energy transition, and sustainability.
The ceremony also included a speech by Professor Dr Cornelius Herstatt on « Sustainable, frugal innovation: the way out of the dilemma between growth and environmental protection? »
In his closing speech, Lex Delles, Minister for the Economy, SMEs, Energy and Tourism, emphasised the importance of innovation and research for the development and diversification of the country’s economy, and underlined FEDIL’s long-standing commitment to innovation. He in turn congratulated the winners, who were presented with their diplomas, a trophy and films made especially for the occasion to illustrate their respective projects.
IEE S.A. – « Laminated busbar connector »
Innovation Award 2024 in the « Product » category
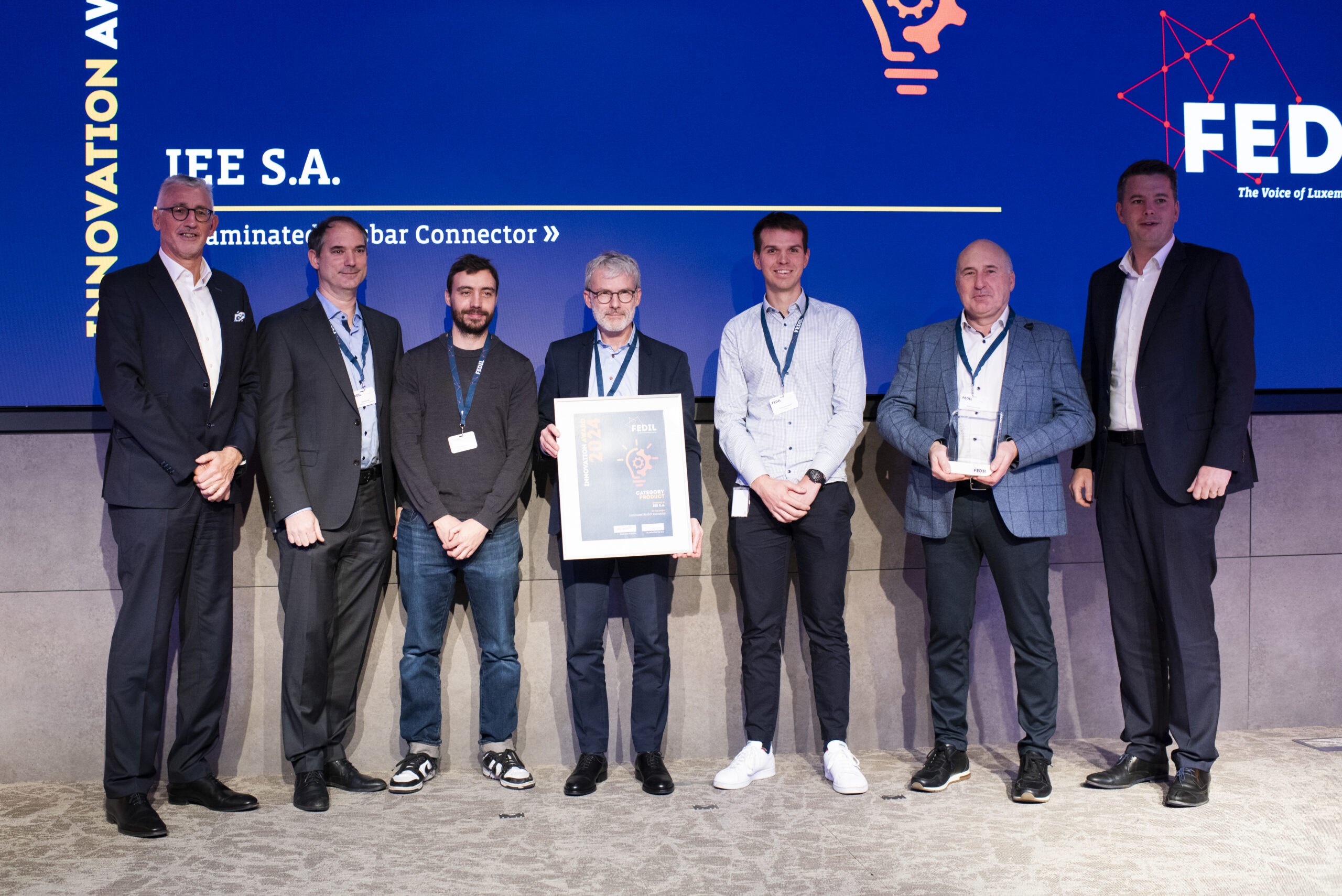
IEE S.A., a world leader in the development of smart sensing solutions and the manufacture of printed hybrid electronics and other sensing technologies for automotive and other markets, has developed an innovative « Laminated Busbar Connector » that will be used primarily in the batteries of electric vehicles (EVs).
This flexible, compact and lightweight busbar connector is a hybrid solution of printed electronics combined with conventional electronic assembly and interconnection elements, integrating multiple functionalities such as voltage monitoring, cell balancing, temperature sensing, electrical isolation and busbar connection in one part.
Design and engineering can benefit from the simplicity of the system. The use of pre-validated and standardised busbar connectors enables better value for money and speeds up the product development process. In addition, this innovative cell contact system requires only a single laminated busbar connector to be handled, rather than multiple components. This allows for a higher level of automation in manufacturing, increasing production efficiency and reducing manufacturing costs.
Compared to traditional cabling in EV batteries, the solution designed by IEE takes up less space, leaving more room in the battery pack for the cells that charge the electricity. This means that the driving range of the vehicle is increased.
Customisation is another important aspect of the product. IEE offers a modular technology kit with the capacity to meet almost any customer’s specific cell assembly requirements. In addition, the compound is compatible with both single-side and double-side bonding cylindrical cells, with clear advantages for cell-to-pack configuration. This adaptability is a key feature that makes the IEE system fit for wide market acceptance.
All in all, the development of IEE, which has been entirely carried out by the team in Luxembourg, capitalises strongly on the cost efficiency advantage, reducing battery production costs and ultimately making electric vehicles more affordable – paving the way for a more sustainable transport future.
Beyond the automotive sector, the features and benefits of the Laminated Busbar Connector can also be extended to energy storage, grid storage and industrial battery applications, which are key to the energy transition.
Husky Technologies – « Plate line automation »
Innovation Award 2024 in the « Process » category
Husky Technologies, a leading global technology provider of injection molding systems and services for the food and beverage, consumer goods, and medical device industries, has implemented an innovative Plate Line Automation project that enables enhanced operational efficiency, product quality, employee productivity and resource utilisation.
This Industry 4.0 innovation consisted of integrating three major advanced technologies in the production of small base plates for their molds, thereby consolidating the process in one single, versatile automated machine, reducing set-up and throughput times and meeting high accuracy requirements.
Firstly, the project involves the use of a self-propelled 5-tonne Automated Guided Vehicle (AGV) prototype, developed by DMG Mori Deutschland, to deliver pallets directly to the milling centre. Compared to traditional pallet handling, this automates transport, reduces transfer times, minimises floor space requirements and ensures safety, thereby increasing overall process efficiency.
Secondly, the project includes fully automated loading and unloading of long tools for deep hole drilling directly into the milling machine. This new tool handling solution eliminates any manual intervention previously required, streamlining the process, ensuring precision and increasing spindle time. The system also monitors tool life and availability.
Thirdly, the implementation of digital twin technology and tool analysis software enables real-time simulation and analysis of the machining process. This development enables precise detection of manufacturing defects, proactive quality control measures and continuous optimisation of the machining process and product quality. It is worth noting that the use of digital twins is a novelty in the production of customised parts.
The high degree of automation enables operators to shift their focus from routine tasks, such as part transport, manual tool removal and insertion, etc., to value-added activities such as high-precision machining, thereby improving overall productivity and the operator-machine ratio in manufacturing.
This holistic approach to transforming a manufacturing process demonstrates the potential of Industry 4.0, using advanced robotics and cutting-edge software like digital twin technology. Husky Technologies has already expanded the concept by integrating two large milling centres into the tool automation. In the future, the company plans to replicate the production concept in other manufacturing facilities around the world.
Creos Luxembourg S.A. / DataThings S.A – « Kopr: The AI twin of the smart grid »
Innovation Award 2024 in the « Digital / AI » category
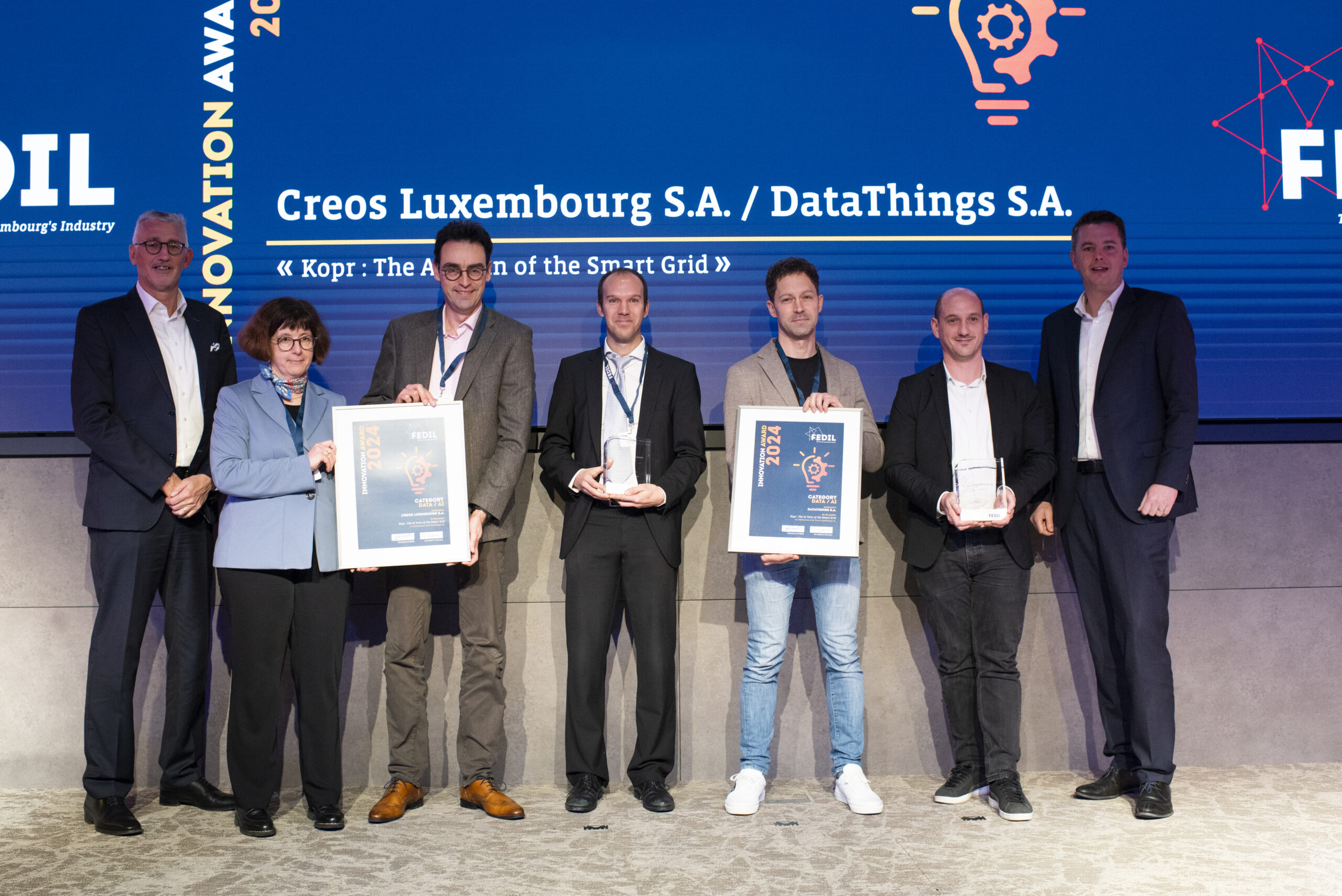
Kopr Twin is a ground-breaking Al-driven digital twin solution designed to revolutionise the management and optimisation of electricity grids.
The development of Kopr has been a collaborative effort: CREOS Luxembourg led the initial ALVA project, providing data from existing systems along with the technical and functional requirements to ensure the solution met the practical needs of grid operations. CREOS tested the beta versions of the system and managed the rollout of the final product. The Luxembourg startup DataThings contributed its proprietary technology, which consists of a new type of database: a programmable temporal graph (“GreyCat technology”) that enables to process massive amounts of data on small local IT infrastructures. Commercialised under the name Kopr Twin, the ALVA project has been developed from scratch in Luxembourg, making it 100% “Made in Luxembourg”.
Kopr offers significant improvements in grid reliability and operations through real-time monitoring and predictive analytics, enabling proactive problem mitigation. Kopr uses advanced digital twin technology to create a virtual replica of the grid that mirrors its real-time state. This digital twin leverages history to enable continuous monitoring, simulation, and optimisation of grid operations, offering a holistic view of grid health and performance and anticipating issues before they occur.
At the heart of Kopr are machine learning algorithms that enhance predictive capabilities. These algorithms learn from historical and real-time data to improve the digital twin’s accuracy in predicting consumption and generation patterns, thereby optimising grid management strategies and supporting sustainable energy integration, aiding in environmental goals and carbon footprint reduction. The solution also provides cost savings by identifying efficiency opportunities and deferring unnecessary investments. It facilitates easy access to vital information and actionable insights to improve decision making.
Kopr features an intuitive, user-friendly interface that provides grid operators with easy access to comprehensive visualisations and actionable insights. This design simplifies complex data interpretation and facilitates effective decision making for grid reconfigurations, maintenance planning, and investment strategies. The integration and visualisation of data from multiple grid systems in Kopr enables generalist staff to gain insights in the grid systems dynamics that were previously only available to specialist staff trained on the expert grid systems.
The system is designed to integrate seamlessly with existing grid systems and infrastructure, requiring minimal additional investment and enabling rapid deployment. Kopr excels in high-resolution data processing, providing near real-time insight and detailed analysis of grid performance on modestly-specified IT infrastructure, enabling it to run on standard laptops or desktop PCs.
In addition, Kopr’s scalability and flexibility allow its deployment across different grid scales, from local to national. The country-wide deployment of a complete digital twin at this level of granularity is unique in Europe and the world. Beyond the initial success with CREOS, Kopr Twin is currently being promoted through several pilot projects with various Distribution System Operators (DSOs) across Europe. These pilots are a crucial step towards wider commercial adoption and demonstrate the growing interest and confidence in Kopr’s capabilities.
CTI Systems S.À R.L / Gradel S.À R.L. – « On Board Cargo Loader »
Innovation Award 2024 in the « Engineering Excellence » category
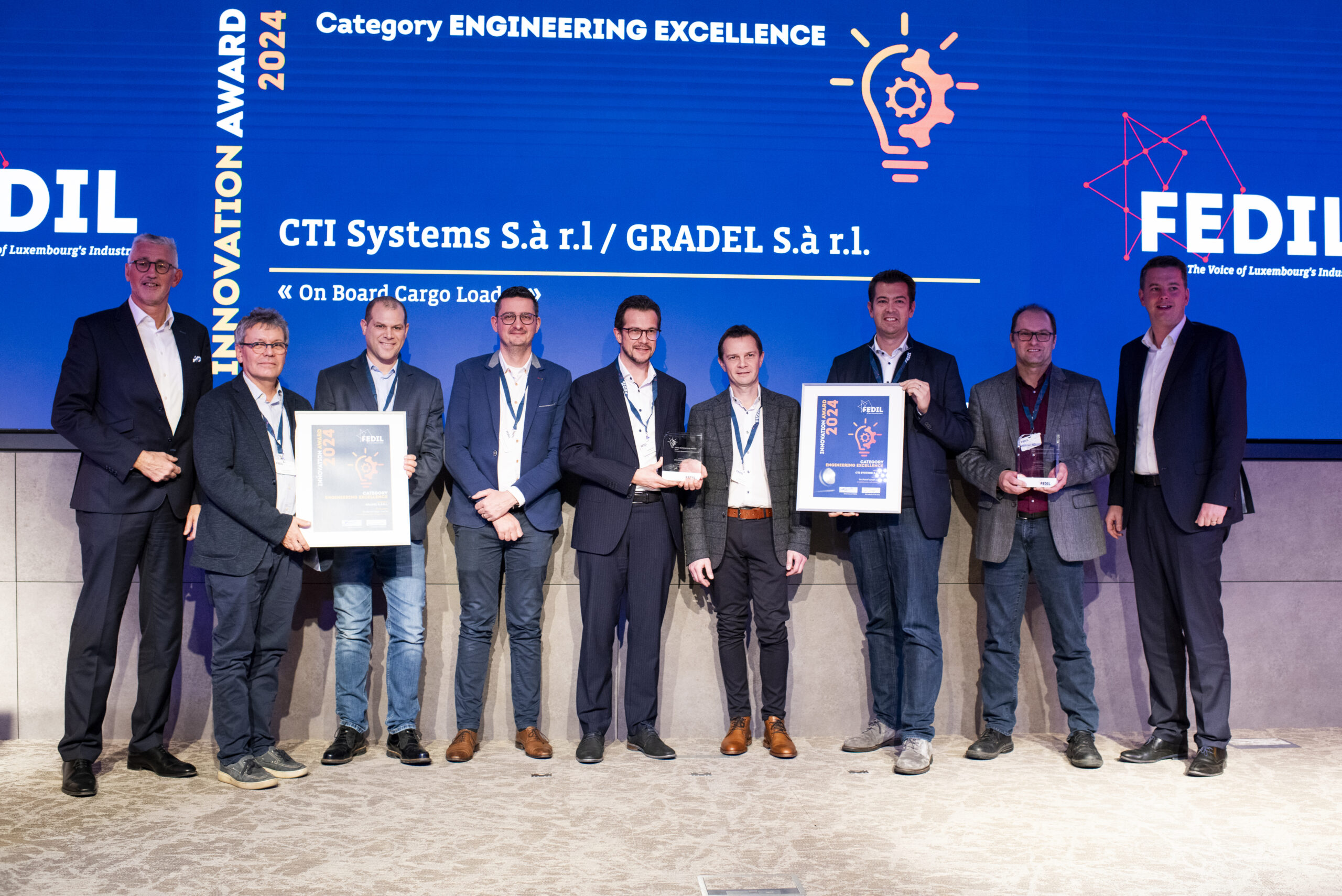
As a renowned material flow specialist, CTI Systems, in close cooperation with Gradel, has developed and produced the so-called “On Board Cargo Loader”, a unique mobile loading equipment for the Beluga freighter, manufactured and operated by Airbus.
Following Airbus’ decision to use its five Beluga aircraft in a future programme for the commercial transport of bulky and heavy payloads, a solution had to be found to load and unload the aircraft at all potential airports, which obviously lack special stationary loading infrastructure for such « giants ». In the case of the Beluga fleet, the cargo area is located above the cockpit level, resulting in a loading height of approximately 5 metres above ground level for a cargo hold that is 39 metres long, 7.1 metres wide and 6.7 metres high. It should be noted that the cargo logistics at the various Airbus production sites is handled by means of stationary loading stations designed, manufactured and installed by CTI Systems.
Airbus ultimately chose CTI Systems to design, build and put into operation three On Board Cargo Loaders (OBCL) that would fly with the cargo on the same aircraft. The On Board Cargo Loader unloads itself from the aircraft after landing and then in a fully automatic way aligns itself to the aircraft and the ground with 6 degrees of freedom. It can load up to 23t of cargo with a length of 10m and a cross section of 7.1 x 6.7m, the widest cross section on the market. It retracts into the aircraft after the payload has been transferred from/into the aircraft. The weight of the OBCL was set at 9t maximum. To achieve this, high-strength materials (stainless steel, aluminium and carbon steel) and CFRP (carbon fibre reinforced polymer) were required. The OBCL is suitable for outdoor use and can withstand temperatures from -40°C to +60°C at some destinations. The overall complexity was the highly innovative combination of the required ultra-lightweight construction and the pairing of the different materials, taking into account statics in many different load cases, stability, weather resistance, temperature expansion, fire resistance, etc. In addition, the high-precision positioning to the aircraft in the harshest weather conditions requires the most accurate measurement technology and permanent and simultaneous control of up to 12 drive units.
Gradel, a specialist in ultra-light structures, both metallic and using the continuous filament winding process of its GRAM composite technology, was asked by CTI Systems to carry out finite element studies with the aim of reducing the weight to 8,600 kg. Materials with completely different behaviours were combined to achieve a lightweight design, yet stiff enough to safely carry a payload of 2.5 times its own weight, a ratio far above the usual industrial standards in load handling technology.
In addition, the entire process and equipment was found to be subject to EASA certification requirements, as the OBCL is considered to be flight hardware. This means that the OBCL must meet all the requirements of the aviation regulations, e.g. with regard to vibrations, accelerations, temperature fluctuations, pressure fluctuations, etc.
The knowledge gained from this very complex engineering task can be applied by both CTI Systems and Gradel to other projects in the aerospace and defence sectors. This special mission has thus become a real light tower project for both companies.