Le 27 novembre 2018 a eu lieu la 23e édition de la cérémonie de remise du Prix de l’Innovation de la FEDIL, en présence de nombreux invités, des membres du jury ainsi que des lauréats de la promotion 2018. Le Prix de l’Innovation de la FEDIL est organisé traditionnellement tous les deux ans en alternance avec le Prix de l’Environnement et permet d’honorer, depuis 1982, les efforts des entreprises luxembourgeoises en matière d’innovation et de recherche.
Dans son mot de bienvenue, le président de la FEDIL, Nicolas Buck, a souligné que le Prix de l’Innovation a vocation à conférer toute la visibilité qu’ils méritent aux responsables des activités de recherche et d’innovation dans les entreprises : les ingénieurs, les techniciens, des personnalités passionnées par les métiers de l’ingénierie et des sciences. Sans ces personnes et leur enthousiasme pour la recherche et l’innovation, il n’y aurait pas de progrès technique, pas d’amélioration de la productivité, et par conséquent pas de développement économique et de croissance du bien-être de notre pays.
Pour la promotion 2018 du Prix de l’Innovation, le jury a décidé d’attribuer quatre prix parmi une vingtaine de dossiers de candidature introduits.
Les lauréats 2018
- Le Prix de l’Innovation dans la catégorie « Process » est attribué à Goodyear pour le projet « Vacuum Cure Technology ».
- Le Prix de l’Innovation dans la catégorie « Product Engineering » est attribué à Cebi Luxembourg S.A. pour le projet « Blow-by Heater ».
- Le Prix de l’Innovation dans la catégorie « SME » est attribué à l’entreprise VIRELUX Inspection Systems pour le projet « Optifrag – Contrôle automatique de fragmentation des vitrages automobiles ».
- Le Prix de l’Innovation dans la catégorie « Start-up » est attribué à l’entreprise DocUnify pour le projet « AdminTech ».
Goodyear
La vulcanisation de pneus sous vide
La fabrication de pneus se fait traditionnellement en deux étapes: la construction des pneus suivie de leur vulcanisation.
Au cours du processus de construction, différents composants et matériaux sont assemblés pour former le pneu « vert », c’est-à-dire non vulcanisé.
Pendant le processus de vulcanisation ou de cuisson du pneu, le pneu vert prend sa forme finale, poussé par une vessie dans un moule segmenté et chauffé qui est installé dans une presse. Le dessin de la bande de roulement et l’estampage des flancs sont ainsi créés et le caoutchouc est vulcanisé.
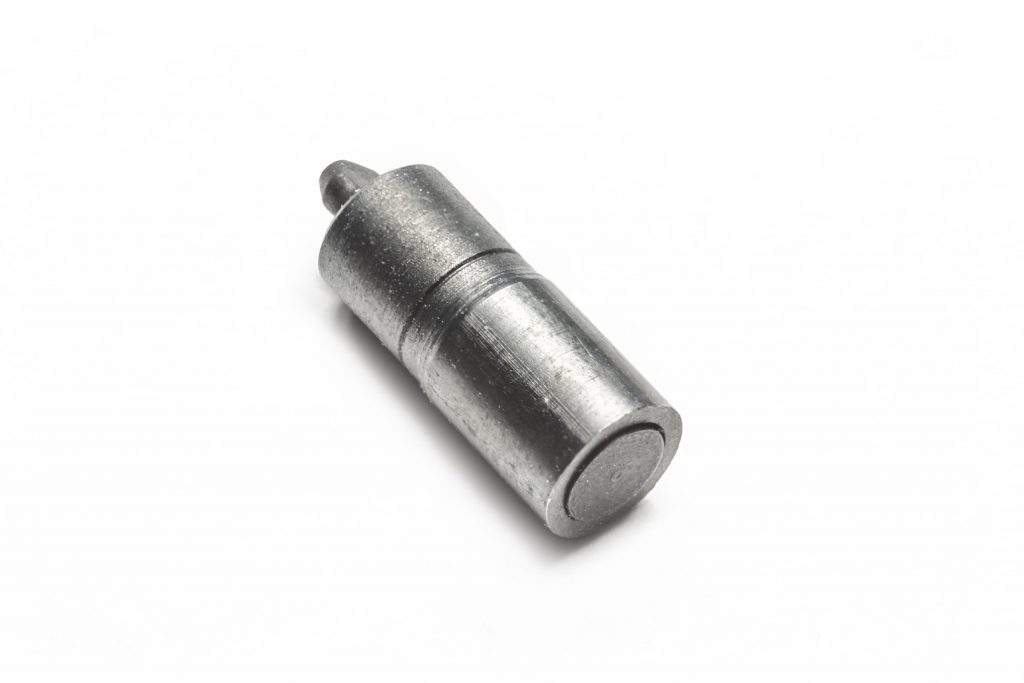
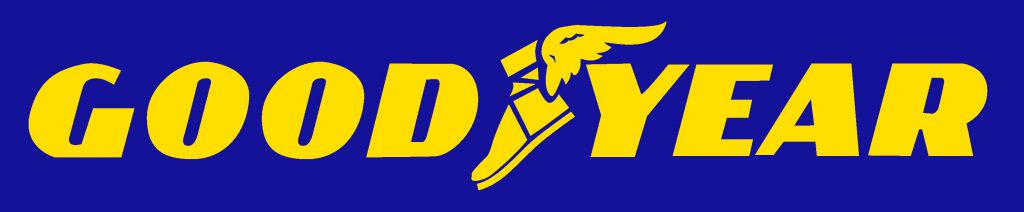
Lors de la cuisson, l’air emprisonné entre le pneu et le moule doit s’échapper par de nombreux évents. Une technique pour évacuer cet air enfermé consiste à insérer des valves d’aération dans les segments du moule qui laissent échapper l’air, mais pas le caoutchouc.
Le nombre d’évents dans un moule varie entre 3.000 et 10.000 en fonction de la dimension et du type de pneu, ainsi que de la complexité du dessin de la bande de roulement.
Ces évents laissent des « cheveux » ou des petites marques sur le pneu fini. Ces « cheveux » sont enlevés à l’inspection finale. De plus, lorsqu’une des bouches d’aération est obstruée, l’air « emprisonné » empêche le flux correct du caoutchouc, ce qui a un effet négatif sur l’aspect final du pneu.
La nouvelle technologie de vulcanisation de Goodyear extrait l’air du moule non pas par des évents, mais grâce au vide appliqué avant le cycle de cuisson. Pour ce faire, le moule est relié à un système de pompage qui évacue l’air lors du gonflage de la vessie. Ceci permet de réduire nettement le nombre de valves d’aération.
Les avantages de la technologie de vulcanisation sous vide sont multiples :
- L’aspect final du pneu est nettement amélioré, parce qu’il n’y a plus ou beaucoup moins de trous d’aération et par conséquence de « cheveux » ou de marques sur les pneus. Ceci améliore l’aspect qualitatif, ainsi que la satisfaction des clients.
- La technologie de vulcanisation sous vide nécessite environ 300 de ces évents, comparé à 3.000 à 10.000 en cuisson conventionnelle. L’économie moyenne réalisée par moule est d’environ 10 %, ce qui se traduit par une économie de 3.000 à 4.500 d’EUR selon la complexité du dessin de la bande de roulement.
- Les coûts de nettoyage et d’entretien des moules sont également moindres, parce que :
• les moules « à vide » peuvent être nettoyés plus facilement et plus rapidement en raison de l’absence de valves d’évent.
• le risque d’obstruction des valves est nettement diminué, ce qui réduit le nombre de réparations en cas de problèmes. - La flexibilité dans la conception des dessins de profils est améliorée, parce que l’absence d’évents donne un plus grand degré de liberté dans la conception de la bande de roulement et de la paroi latérale.
La technologie de vulcanisation sous vide a été développée par les ingénieurs du Goodyear Innovation Center (GIC*L) à Colmar-Berg, de l’Engineering Group et de la Mold Plant et elle a été évaluée dans les laboratoires du ‘Innovation Prototype Lab’ (IPL) à Colmar-Berg.
Le développement comprenait la conception du moule sous vide, la spécification d’un système de pompage et de contrôle du vide et la définition d’un nouveau cycle de cuisson du procédé sous vide. Cette technologie a été validée dans l’usine de fabrication des pneus prototypes du GIC*L avant d’être introduite dans d’autres usines européennes de Goodyear.
Tous les moules sous vide sont produits à la Mold Plant à Colmar-Berg.
La technologie de vulcanisation sous vide est utilisée dans la production de pneus hiver pour véhicules SUV et sera appliquée sur les nouveaux pneus été ultra haute performance produits dans l’usine de production de pneus prototypes du GIC*L.
La technologie de vulcanisation sous vide nécessite une nouvelle configuration de moule dans laquelle plusieurs joints et barrières étanches à l’air sont installés et intégrés pour prévenir les fuites d’air. Ces joints et barrières doivent supporter les températures élevées de fonctionnement du moule jusqu’à 200°C, la pression interne élevée du moule jusqu’à 8 bars et l’ouverture et la fermeture fréquentes des moules pendant les opérations de cuisson (en moyenne toutes les 10 minutes pour un pneu voiture).
De plus, une pompe à vide maintient la sous-pression et un système de contrôle surveille la performance, la sécurité et la qualité du vide et du bon fonctionnement.
Le coût de la pompe à vide et du système de contrôle est d’environ 5.000 d‘EUR par presse. Il s’agit d’un investissement unique. Une fois qu’une presse est convertie à la polymérisation sous vide, elle peut traiter tous les moules de type vulcanisation sous vide.
Le projet a démarré en 2012 et la 1ère application a eu lieu en 2016. Depuis lors, sept usines européennes Goodyear utilisent cette nouvelle technologie de vulcanisation et environ 100 moules ont été fabriqués avec la nouvelle technologie de cuisson sous vide. Depuis 2012, le volume de production de pneus vulcanisés sous vide s’est considérablement accéléré avec plus d’un million de pneus produits, dont un peu plus de 500.000 en 2017 seulement.
CEBI
Réchauffeur piquage tubulure Blow-by
Avec plus de 3500 employés dans le monde entier, le groupe Cebi est composé de 11 sites de production situés dans 8 pays différents (Luxembourg, Suisse, Italie, Espagne, Pologne, Mexique, Brésil et Chine) et de 7 antennes commerciales. Cebi développe et produit des composants électromécaniques pour les plus grands constructeurs automobiles ainsi que pour les principaux fabricants d’appareils électroménagers et d’installations industrielles.
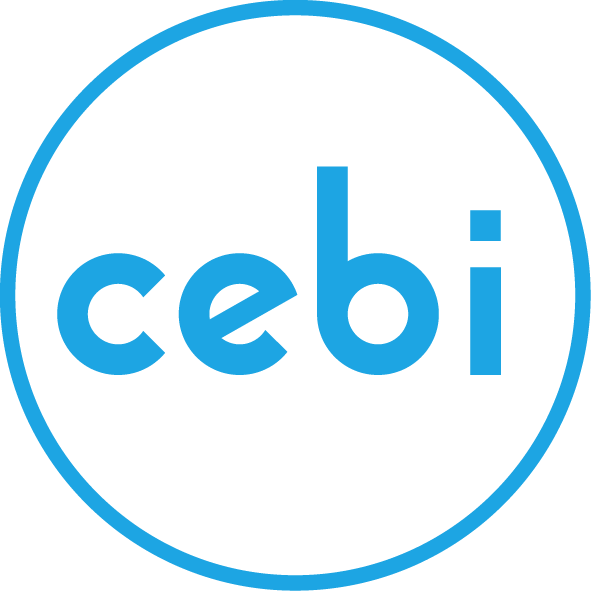
Fondé en 1976 sous le nom ELTH, Cebi Luxembourg S.A. est l’un des plus anciens sites du groupe. Dès sa création, cette société s’est imposée dans la fabrication de thermostats bimétalliques et de sondes de température pour lesquels le groupe est actuellement leader européen. Depuis, l’usine s’est largement agrandie et emploie plus de 650 salariés. Cebi Luxembourg réalise une production moyenne de 300 000 pièces finies par jour. On y retrouve des capteurs de température, des sondes de niveau, des réchauffeurs gasoil et habitacle ainsi que des systèmes de lavage pour pare-brises et phares.
Suite à la concurrence toujours croissante dans le monde automobile, Cebi est amené à sans cesse innover et optimiser ses produits. Le projet « Blow-by Heater » concerne un petit composant sous forme de tube chauffé électriquement servant à éliminer la glace qui peut se former dans un conduit de ventilation du bloc moteur. Il trouve son utilisation surtout dans les régions froides de l’Europe du Nord, de l’Asie et du continent nord-américain et il y assure la longévité et la conformité aux normes des moteurs à combustion essence et diesel.
L’objectif du projet était de revoir intégralement le design de ce composant électromécanique pour le rendre plus léger, plus compact et lui donner une plus grande souplesse d’adaptation aux exigences clients. Pour atteindre cet objectif, Cebi s’est servi de la simulation thermique et d’une série d’essais en chambre climatique pour arriver à une performance maximale et une complexité réduite tout en optimisant l’efficience énergétique et l’encombrement. Le résultat est une réduction de la masse de 36 % et une réduction du nombre des composants de 40 %. Protégé par 3 brevets, ce développement a produit un composant compact, léger, écologique et très flexible à la demande du client.
À côté du design de la pièce, ce projet a également permis de faire un pas supplémentaire dans la verticalisation et l’automatisation des processus de production. La verticalisation, c’est-à-dire le contrôle de la chaîne de production en partant de la matière première jusqu’à l’assemblage final du produit, a toujours été le point fort de la société, contrairement à la concurrence qui a plus souvent recours à la sous-traitance. Dans le cadre du projet « Blow-by Heater », l’opération de surmoulage du tube central métallique est effectuée par une presse d’injection plastique horizontale équipée d’un robot pour le chargement du tube et le déchargement de la pièce finie, le tout en automatique. La même chose s’applique pour le connecteur électrique.
Ensuite, la partie assemblage a aussi été rationalisée pour optimiser les flux matières. Contrairement à la première génération, la nouvelle conception de ce réchauffeur permet d’assembler et de contrôler le produit en un seul passage sur la ligne de montage. L’étanchéité de la partie électrique est assurée par une soudure plastique ultra-son, empêchant toute pénétration d’éléments provenant de l’ambiance moteur. Un contrôle caméra de la soudure permet de garantir le niveau de qualité demandé par les clients, en profitant du savoir-faire sur les sondes de température et les réchauffeurs gasoil qui se servent déjà de cette technologie.
Cebi va vendre plus de 500.000 réchauffeurs blow-by d’ici fin 2019, pour des voitures du monde entier mais surtout aux Etats-Unis et en Asie. Des contrats de fourniture avec des clients supplémentaires, dont les plus grands constructeurs du monde, sont en discussion.
Le Luxembourg est un pays à coût de fabrication élevé. Face à la concurrence des pays de l’Est ou de l‘Asie, il faut être d’autant plus innovateur pour rester compétitif. C’est l’une des raisons pour laquelle Cebi a investi énormément dans l’automatisation des machines et dans de nouveaux équipements à la pointe de la technologie. Cebi prend également part à de nombreux projets ambitieux tels que l’Industrie 4.0. Les produits de l’ensemble du groupe sont sans cesse revus et optimisés pour assurer une amélioration constante et permettre une compétitivité plus grande. Ce processus est piloté par le centre de compétences localisé à Steinsel qui est en charge de la conception, de la commercialisation et de l’industrialisation de l’entièreté des produits fabriqués au Luxembourg et aussi d’une partie des produits fabriqués dans le reste du monde. Un agrandissement de ce centre est d’ailleurs en cours afin de faciliter la collaboration entre les spécialistes produits et processus et pour offrir davantage de place pour des nouvelles installations d’essais laboratoire.
VIRELux
Contrôle automatique de fragmentation des vitrages automobiles
La norme ECE R43 régit le comportement d’un verre automobile trempé en cas d’impact afin de garantir la sécurité des personnes. Pour vérifier le respect de cette norme dans le domaine du verre trempé des vitrages automobiles, des tests destructifs dits « de fragmentation » doivent être effectués. Ils consistent à casser le vitrage par un choc ponctuel. Les fragments, après fracture du verre, doivent répondre à des critères précis de taille (longueur et surface) et de densité de répartition.
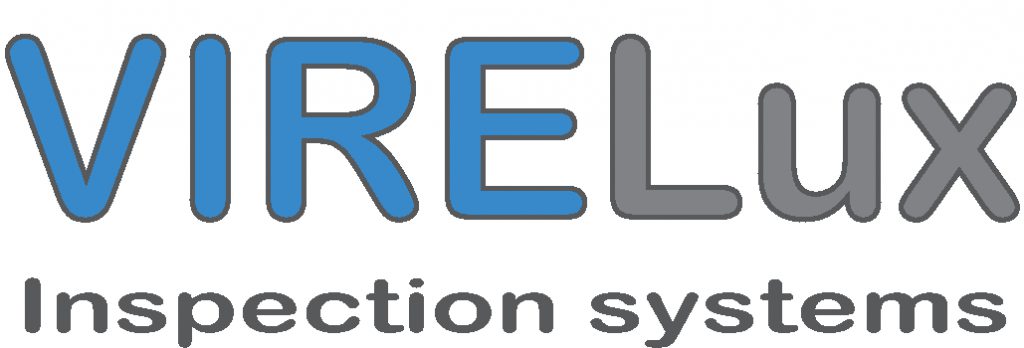
Le comptage des fragments est très fastidieux, car il est réalisé manuellement, et représente de fortes contraintes et limitations. De plus, la subjectivité du comptage et le mode opératoire d’analyse, réalisé en transmission à partir d’un film papier photo insolé par une source d’éclairage, rendent la procédure actuelle obsolète au point que tous les fabricants recherchent depuis plusieurs années une solution de substitution qui permette le comptage automatique.
Le projet ‘Optifrag’ vise à remplacer cette méthode de comptage manuelle sur film papier par une solution de contrôle optique automatisée.
La fréquence de ces contrôles est importante dans la mesure où ils doivent être effectués à chaque nouveau démarrage d’une séquence de production, pour chaque nouveau réglage des fours de trempe, chaque début de poste, et chaque géométrie de vitrage à différentes positions d’impacts, ce qui constitue des dizaines de vitrages fragmentés par jour de production.
Pour effectuer ce test, le vitrage à fragmenter est soutenu par un second vitrage de même géométrie. Un film photo papier est placé entre les 2 vitrages et, après fragmentation du vitrage supérieur, le film photo est insolé dans une chambre noire. La lumière passe au travers du vitrage et est
« bloquée » par les frontières des fragments du vitrage.
Les films sont ensuite développés dans une tireuse de plan à l’ammoniaque et sont confiés à des opérateurs spécialisés qui effectuent un comptage visuel des fragments sur toute la surface du vitrage, suivant des critères bien définis et normalisés. Le caractère fastidieux et subjectif du comptage manuel est non sécuritaire et représente un coût de main d’œuvre non négligeable, ainsi que des contraintes dans le réglage des lignes de trempe du verre.
Les opérateurs de contrôle doivent définir, parmi des milliers de fragments, où se situent la zone de plus forte concentration de fragments, la zone de plus faible concentration de fragments, le fragment le plus long et le plus gros.
Cette méthode ne permet pas d’insoler la partie du film en contact avec la sérigraphie (zones noires) des vitrages, ce qui nécessite un comptage direct sur le verre (très difficile à réaliser), et les réseaux de fils de dégivrage et d’antenne bloquent le passage de la lumière, ce qui crée de faux fragments.
L’innovation apportée par ‘Optifrag’ est ce que l’on peut appeler une innovation de rupture dans la mesure où elle supprime l’utilisation du film papier et la remplace par une méthode optique qui permet un comptage automatique objectif des fragments y compris dans les zones de sérigraphie du vitrage.
L’innovation majeure réside dans la capacité à qualifier la fragmentation de façon automatique par une méthode de mesure optique dynamique. La mesure n’est pas réalisée en transmission (au travers du vitrage), mais en réflexion sur la surface convexe du vitrage sur la face opposée de la sérigraphie et des réseaux de fils de dégivrages.
Pour résumer, la solution ‘Optifrag’ permet de :
- Supprimer l’utilisation du film papier actuel
- Mesurer le vitrage en partie externe courbe
- S’affranchir des réseaux dégivrants et des fils d’antenne qui coupent les fragments
- Mesurer les zones noires de sérigraphies
- Mesurer les vitrages non teintés et teintés
- Déterminer automatiquement les zones de plus faible et de plus forte segmentation
- Identifier automatiquement le plus grand et le plus gros segment
- Archiver numériquement les résultats
Ce qui est aussi remarquable dans ce projet en termes d’innovation c’est que VIRELUX a été contraint de développer ses propres sources d’éclairage dynamique LED courbe, ce qui représente une innovation supplémentaire dans l’innovation de la solution de fragmentation. D’un point de vue économique, le produit (Optifrag) s’ouvre non seulement à un marché niche, mais aussi à d’autres applications dans le contrôle d’aspect des surfaces automobiles et aéronautiques, voire à d’autres secteurs.
Ces innovations en cascade ouvrent des perspectives économiques intéressantes dans l’utilisation des solutions d’éclairage dynamique développées.
Le développement de la technologie ‘Optifrag’ a d’abord été réalisé pour le premier fabricant au monde de vitrage (AGC) et la technologie est en passe d’être généralisée chez tous les fabricants de vitrage (Saint-Gobain, NSG / Pilkington, Carlex…).
DocUnify
AdminTech
Quel que soit leur secteur d’activité, ou même leur taille, chaque entreprise est amenée à gérer des processus et documents administratifs de manière quasi quotidienne. Quoique indispensables à leur bon fonctionnement, ces tâches sont souvent répétitives, presque toujours contraignantes et indéniablement chronophages.

Certes, l’optimisation progressive des processus internes permet d’améliorer certains aspects de la gestion administrative, mais les gains s’avèrent rapidement limités et les coûts restent très significatifs, en temps et en argent, pour chaque entreprise.
L’avènement et la familiarisation des entreprises avec les technologies digitales dans le domaine de la communication et/ou des Fintech d’un côté, et la nécessité de réduire leurs coûts de fonctionnement et leur impact écologique de l’autre, laissaient entrevoir un besoin pour des solutions de gestion administrative plus effectives, dites smart. Le marché n’offrant alors aucune solution efficace dans ce domaine, une solution innovante devait alors être créée.
C’est dans ce contexte que le projet Docunify s’est constitué, et par la même occasion, a été créé le secteur de l’Admintech. Le tout, « Made in Luxembourg ».
Créé en 2014, par la rencontre entre des professionnels du secteur des fonds d’investissements, experts dans la gestion des problématiques administratives, et d’un développeur, spécialisé dans la création de plateformes digitales innovantes, Docunify est depuis une solution reconnue, utilisée et plébiscitée dans l’écosystème luxembourgeois.
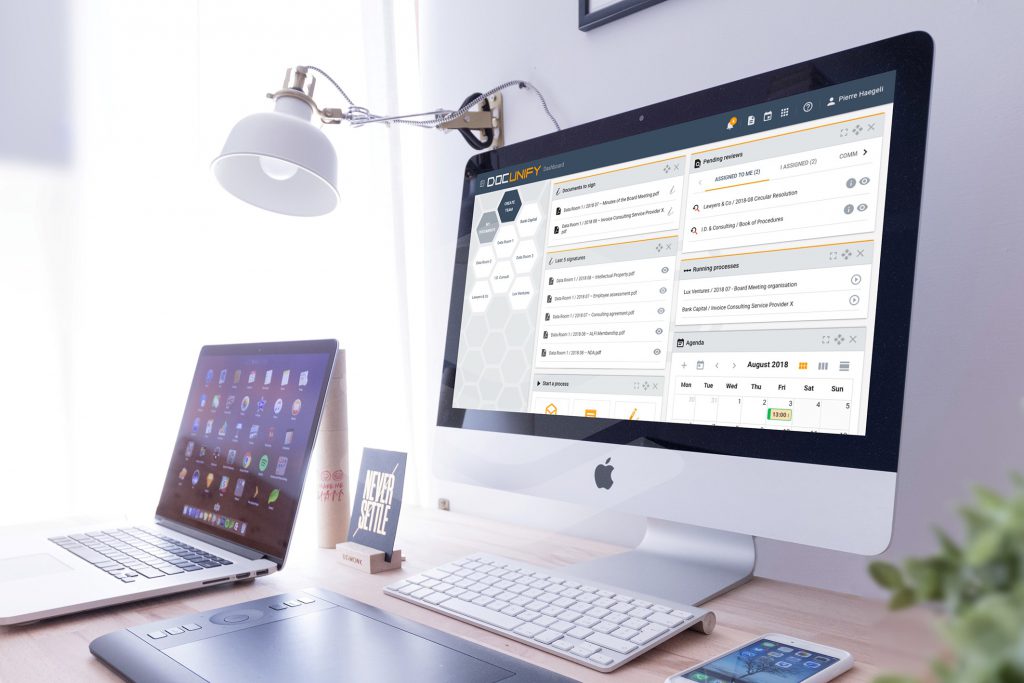
La technologie administrative ou AdminTech, c’est une nouvelle industrie qui utilise les technologies et innovations digitales pour simplifier et améliorer la gestion administrative des entreprises. En d’autres mots, il s’agit de développer le travail collaboratif sécurisé, tout en supprimant le papier qui n’est plus une solution durable aujourd’hui !
Aujourd’hui, Docunify permet à ses clients de réaliser une multitude de tâches administratives, qu’elles soient internes ou externes, de manière totalement digitale. Cela passe par la gestion documentaire, la signature électronique eIDAS, le partage de données, les datarooms, la gestion de boardpacks et/ou l’automatisation de processus administratifs. Demain, un système de vidéoconférence et de chat viendront également rejoindre la plateforme.
Basée sur l’expérience de clients utilisant les solutions AdminTech de Docunify, une entreprise peut espérer améliorer instantanément de 30 à 40 % l’efficacité dans sa gestion administrative quotidienne. À cela s’ajoute, un renforcement de l’image d’une entreprise dynamique et innovante, une réduction du risque d’erreurs ainsi que de son empreinte écologique.
L’un des changements les plus intéressants s’opère en interne, auprès des collaborateurs. Libérés d’une partie de leurs contraintes administratives, ils sont désormais en mesure d’allouer leurs talents à d’autres tâches, davantage créateurs de valeur et plus proche du cœur d’activité de l’entreprise. Cela constitue un avantage compétitif conséquent permettant entre autres, d’accélérer la mise en place de services et projets stratégiques pour l’entreprise mais aussi d’améliorer l’attention et l’expérience client.
La philosophie de développement de Docunify repose depuis les premiers jours, sur la nécessité de mettre la technologie au service du fonctionnement de l’entreprise. Les changements doivent être minimum, l’impact maximum et immédiat. C’est pour cela que Docunify repose sur une WebApp accessible via une adresse sécurisée depuis tout type d’appareil (ordinateur, smartphone, tablette, etc.), à tout moment. L’outil ne nécessite aucune installation préalable, uniquement l’ouverture d’un compte en ligne.
En ce qui concerne la question sécuritaire, au cœur de toutes les discussions stratégique d’entreprises aujourd’hui, les données et documents sont stockés par Docunify – via un « data center » situé au Luxembourg ou ailleurs en Europe, selon le choix du client –, et non sur le terminal utilisé, permettant ainsi de les sécuriser de façon optimale et de répondre aux exigences de confidentialité les plus strictes.
Les dernières récompenses professionnelles, dont le Prix de l’Innovation de la FEDIL 2018, et l’enthousiasme d’une clientèle de plus en plus internationale, permettent à Docunify et à son équipe, composée d’une dizaine de personnes dont une grande partie de développeurs, d’envisager le futur avec excitation et de planifier dès aujourd’hui son expansion à d’autres capitales européennes.